Deep 5-mile-tunnel to a Critical Water Supply Reservoir
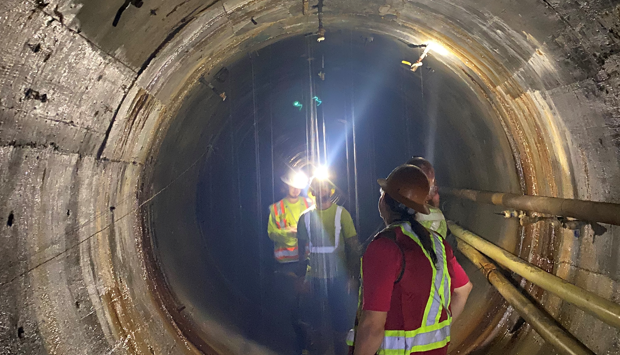
Black & Veatch steps in to help city complete a deep 5-mile tunnel to a critical water supply reservoir
To the public, the marquee feature of Atlanta’s $320 million water supply Program is a former rock quarry that had become a location for shooting movies and television shows.
Repurposed under the program, the quarry is now a 2.4-billion-gallon water supply reservoir and the heart of a new 280-acre city park replete with amenities for recreation and community gatherings.
Unseen is the artery of the program: a five-mile-long tunnel built through bedrock 250 to 500 feet below the city. The tunnel connects the old quarry/new reservoir to two pump stations and two water treatment plants.
Essential to the program’s success was the quality and on-time, on-budget delivery of the tunnel. Which was why, during construction, the city turned to Black & Veatch.
ㅤ
ㅤ
Quarry Conversion
Atlanta’s sole raw water source is the Chattahoochee River. The conversion of the rock quarry into a storage reservoir added a critical, additional source. Storing at least a 30-day supply of water, the reservoir protects against disruption to the availability of Atlanta’s water. It strengthens the city’s resilience and supports its growth.
River to Tap and Stantec Joint Venture served as the program’s lead design firm and civil engineers, with PC Construction and H.J. Russell & Co. as construction managers. Selected for its expertise in deep tunnel projects, Black & Veatch joined the program as the owner’s advisor. The company led the quality control and inspection team during the tunneling and pump station construction, supplying resident engineering, structural guidance, and tunneling, mechanical, electrical, and plumbing expertise through facility commissioning. The company also advised on the project’s LEED certifications and as-built drawings.
ㅤ
Keeping the Tunnel on Track
Waiting until after completion to fully vet the tunnel would have been much more difficult and costly for Atlanta. Joining the award-winning project during construction, however, accelerated the challenge for Black & Veatch. The BV team acted quickly to inspect and evaluate the tunnel’s progress to ensure its quality and keep construction on track.
Sequencing was an example. Grouting, repair, and cleanup work was conducted using access from the tunnel’s two drop shafts and two opposing directions, doubling the activity, and shortening delivery time.
Geologic mapping and daily inspection of the raised-bore shaft also ensured quality construction documentation was available for evaluation of differing site-conditions claims. This helped to reduce undue cost increases.
Additionally, continuous inspection allowed the quality to be monitored as work progressed in a linear fashion. Doing so eliminated time-consuming back-and-forth movement of materials and labor, particularly in the grouting phase. Experienced construction managers were onsite, providing ongoing verification of grouting operations, repair work on the concrete-lined section, and cleaning operations.
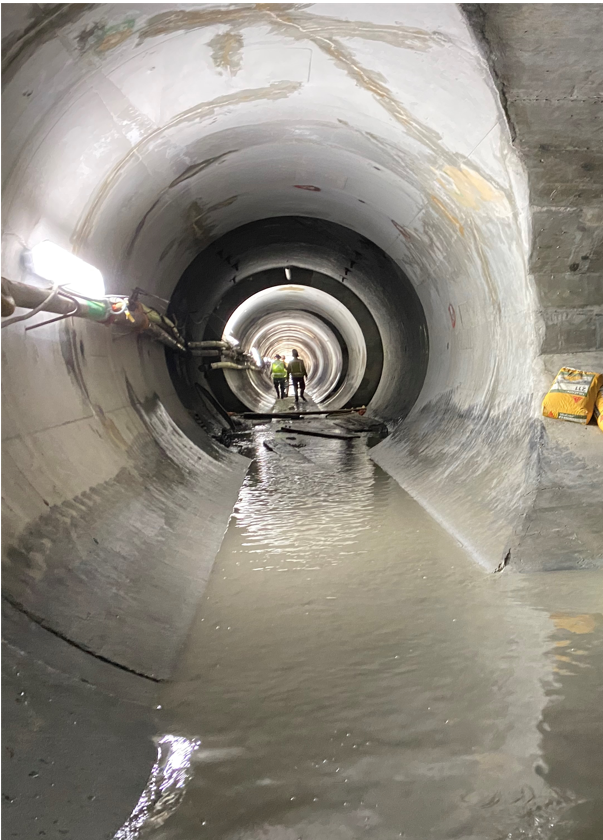
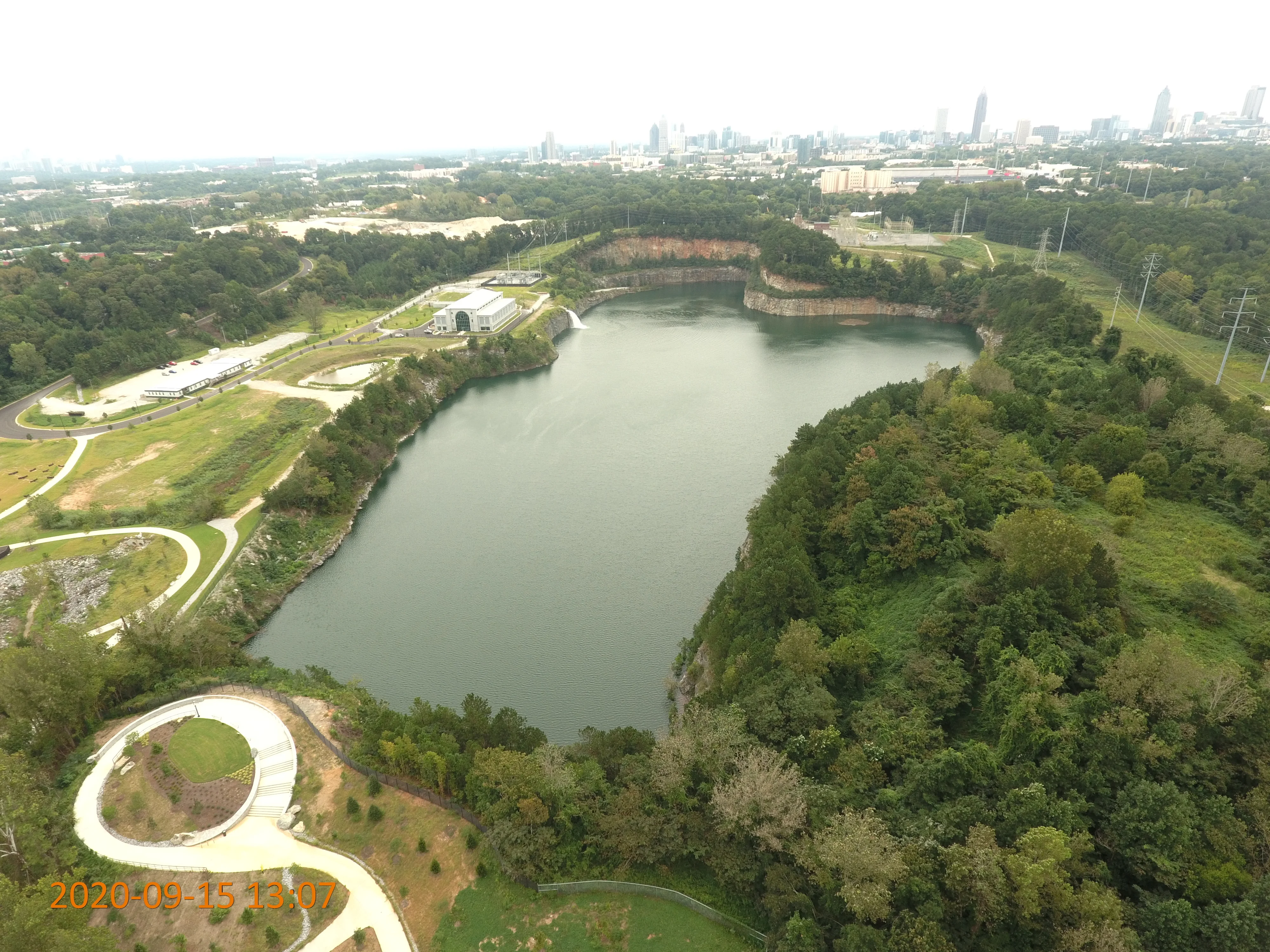
Contact Us
Looking for a partner in innovation?
Let's Talk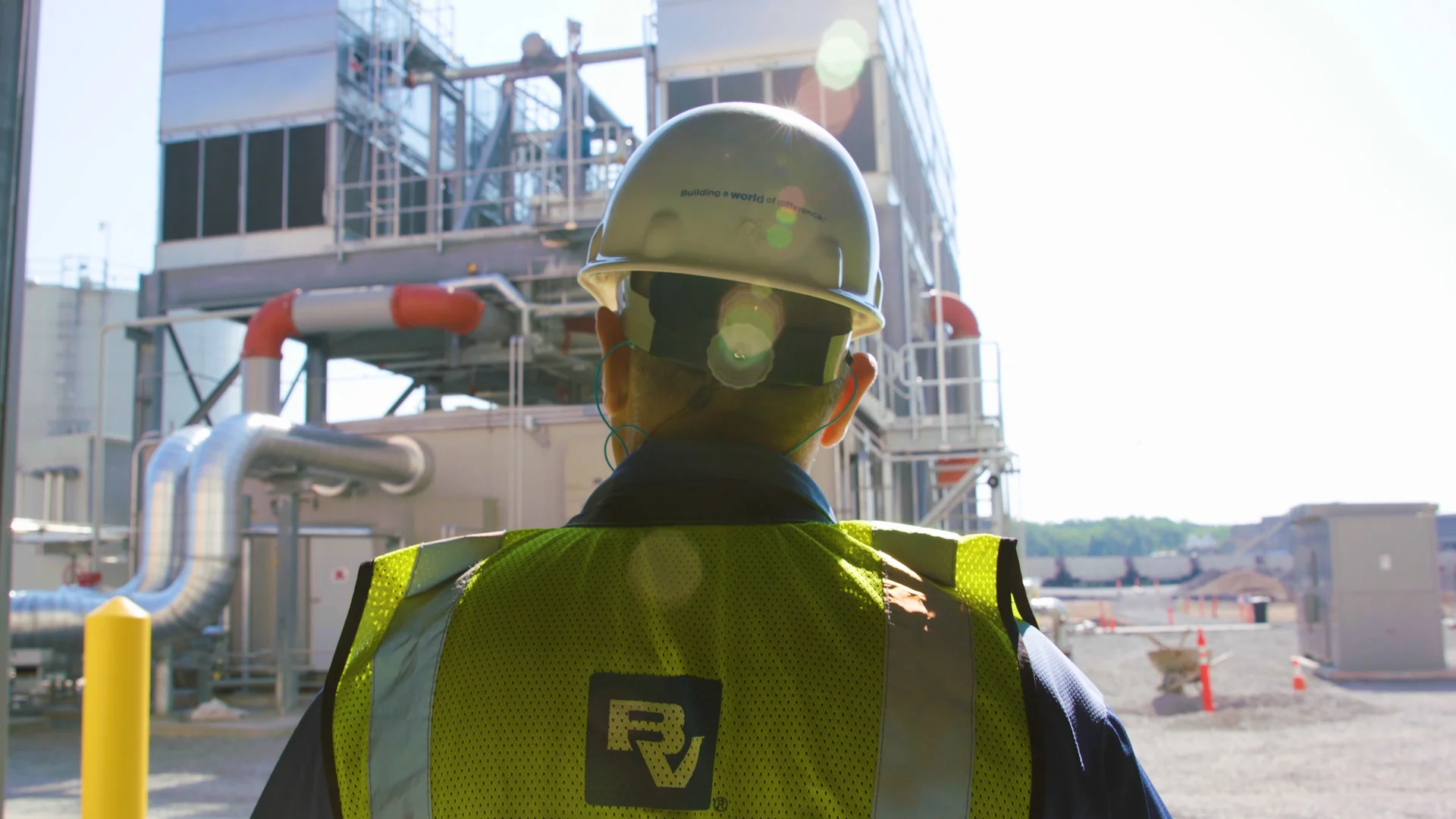