A Solar Success Story
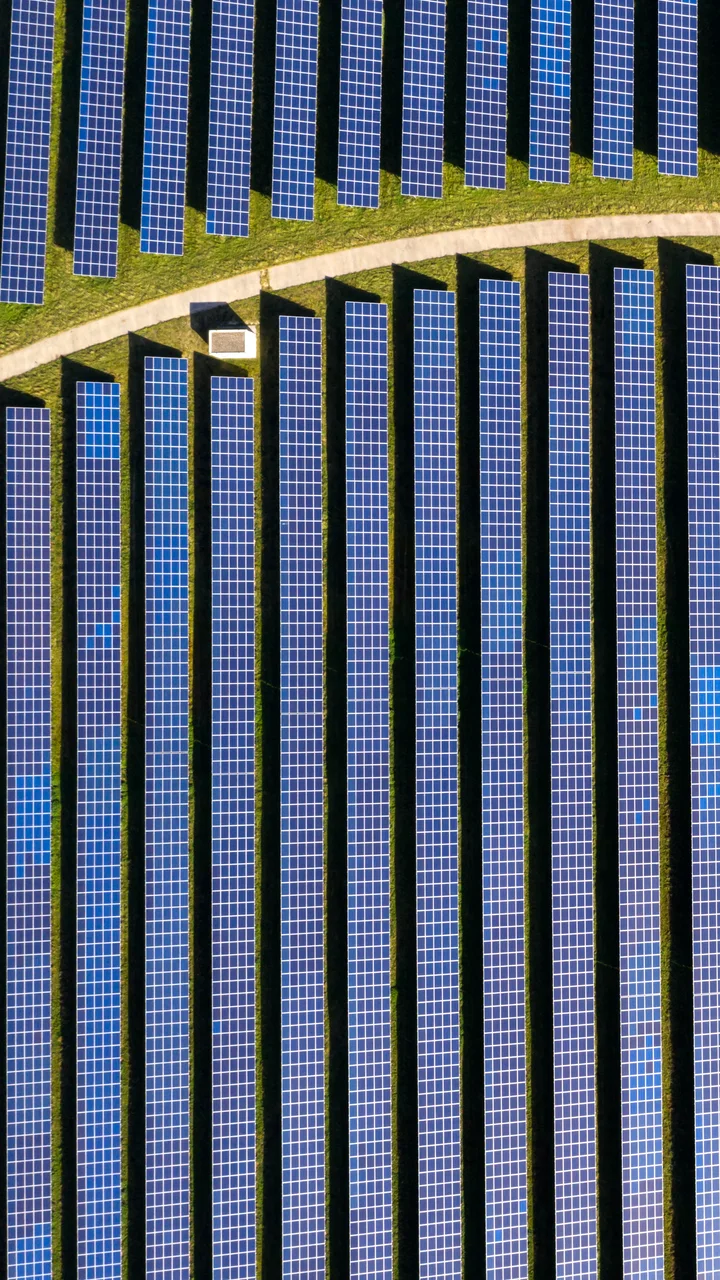
Women-led Construction Management Team Overcomes Site Challenges to Deliver Solar Project on Time
The coastal state solar project had more than its share of challenges. Overcoming them is what distinguished the construction management of three leaders – project controls manager Gina Butler, project field manager Mary Korte and site quality manager Cecelia Chang. Drawing on their diverse expertise and experience, they rallied the team to handle each challenge – the known and unexpected – and added, on schedule, 75 megawatts (MW) of renewable solar power to the utility’s capacity.
The Project
Black & Veatch provided full engineering, procurement and construction (EPC) services for the project, including construction management of modules and inverters procured by the client and select services that were subcontracted.
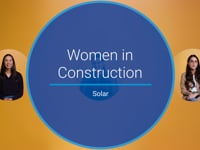
The Challenges
The unexpected came day one from a surprising source: gopher tortoises. Safe removal of the endangered species to another location took three weeks, pushing back the rest of construction.
The tortoises were only the beginning. After they had been safely relocated, construction faced additional surprises.
Some stemmed from the site’s greater-than-anticipated forestation. Clearing required special equipment and more time than scheduled. The team got back on track for the leveling process, but the clearing had revealed more challenges and faced equipment and labor shortages due to nearby solar projects.
The clearing also unveiled a need for an unanticipated wetland crossing that required 400 linear feet of culvert. It was installed with a large drop-off that required specific compaction testing and field engineering, and intense rain required installation to be reworked multiple times. All this created a monthlong delay in piling and installing direct current electrical under cables.
Additionally, the site had to shut down for two direct, late-season hurricane threats. The storm plan dictated that the team clean up the site, tie everything down and board up trailers to ensure the safety of the site and its neighbors. The safety-focused management team also made the decision to implement this plan early, so that those working on site had adequate time to take care of their families and homes before the hurricane hit.
“You know that you're going to lose time, but the important thing is making sure the site doesn't get destroyed and making sure your craft professionals – working hard for you day in and day out – have time to get home, get situated and get their families ready. That's what everyone's thinking of,” Korte said.
As is common in post-COVID projects, the project saw equipment constraints, material delays and long procurement lead times. The project also struggled to maintain the level of craft labor needed to overcome schedule delays created early on. An already tight labor market, a surplus of area projects and the need to ramp up resources meant that Black & Veatch’s training and safety programs were critically important. As new construction professionals came on site, they went through a system of front-line training (a standard Black & Veatch practice). Once they were sufficiently onboarded, professionals would “graduate” from a blue hard hat to an official white Overland Contracting Inc. (OCI) hat. (“I’ve never seen so many blue hats on a project,” Butler said). This continuous program was key to ensuring proper installation, as well as onsite safety.
“It was challenging because you do have so many new people. So it's a lot to take on to try to teach and make sure that we're keeping people safe and that they're doing things the right way; then they don't have to go back and fix something later, which is when you get people really hurt,” Korte said. “But it was also a lot of fun because there's a lot of teaching and coaching involved, which I enjoy.”
The Team
All the challenges meant that the construction management team had to leverage strong working relationships and a singular dedication to achieving their client’s goals.
The project team started with solid relationships; many leadership team members had worked together on previous projects, and that developed relationship kept things positive and moving smoothly even in a high-stress situation. The time crunch meant long hours on site – adding in weekends, 12-hour days and 13-day stretches. Normally, this is when safety can be compromised, but this team’s positive dynamic and focus on safety meant it stayed the course: 222,000 hours worked with no recordable incidents. This largely was due to the team culture set by its leaders.
222,000 Hours
worked with no
recordable incidents
In a male-dominated industry, the leadership team stood out for largely being women, including the project field manager, project controls manager, quality manager, materials manager, office manager and field supervisors.
“We're not the kind of women that you can push around, and that's obviously how we make it through construction,” Chang said. “But we did have a supportive team of the men we were working with, and that's a huge part of it, too. Our bosses support us fully, and that's how we've been able to become as assertive as we have been.”
The project also was a training ground for future construction leaders, with success stories that surfaced for two of the women working in the field. One is going from craft to staff on her next project, as a project coordinator. The other is transitioning from a quality lead to a full-blown quality manager for her own project.
“It was really exciting for all of us to have more women moving up into construction management,” Butler said.
Beyond the onsite construction management, the team had members in Black & Veatch offices and beyond who were instrumental in the project’s success, including home office project controls.
“There were a lot of good working relationships that eased those extra hours. That teamwork mentality and a lot of resilience helped carry us to the finish line,” Butler said.
Conclusion
2022 was a challenging year for construction across the board with post-COVID equipment constraints, material delays and long lead times. This coastal solar project faced all these, in addition to challenges from the natural world.
The teamwork and ingenuity of Black & Veatch’s field construction, construction management and home office employees helped them to figure out creative ways to acquire material, equipment and manpower to deliver the project on time, despite the many obstacles.
The team overcame more than two months of construction setbacks to “hand over the keys” on the original contractual delivery date of Jan. 31, 2023.
Contact Us
Looking for a partner in innovation?
Let's Talk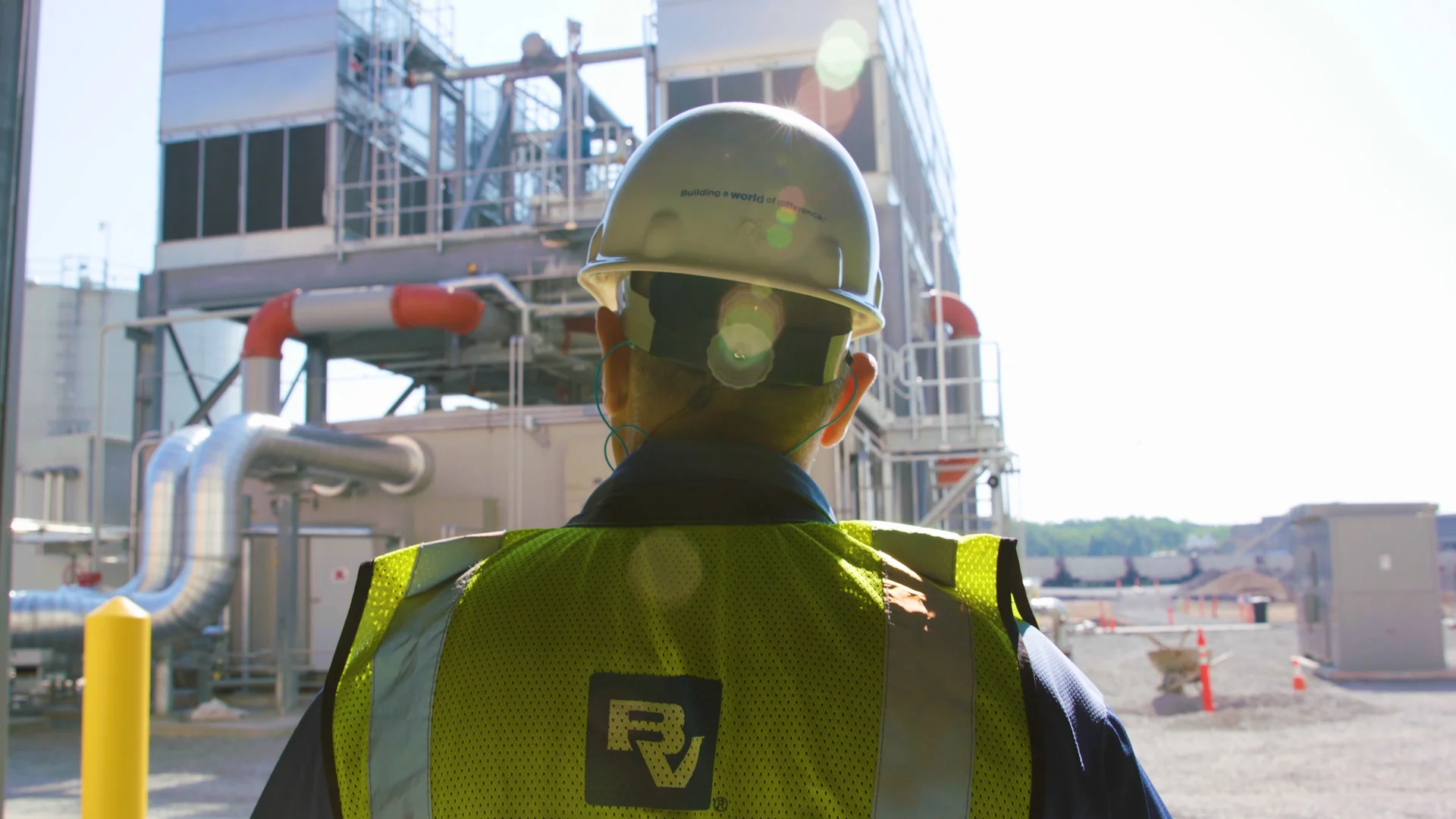